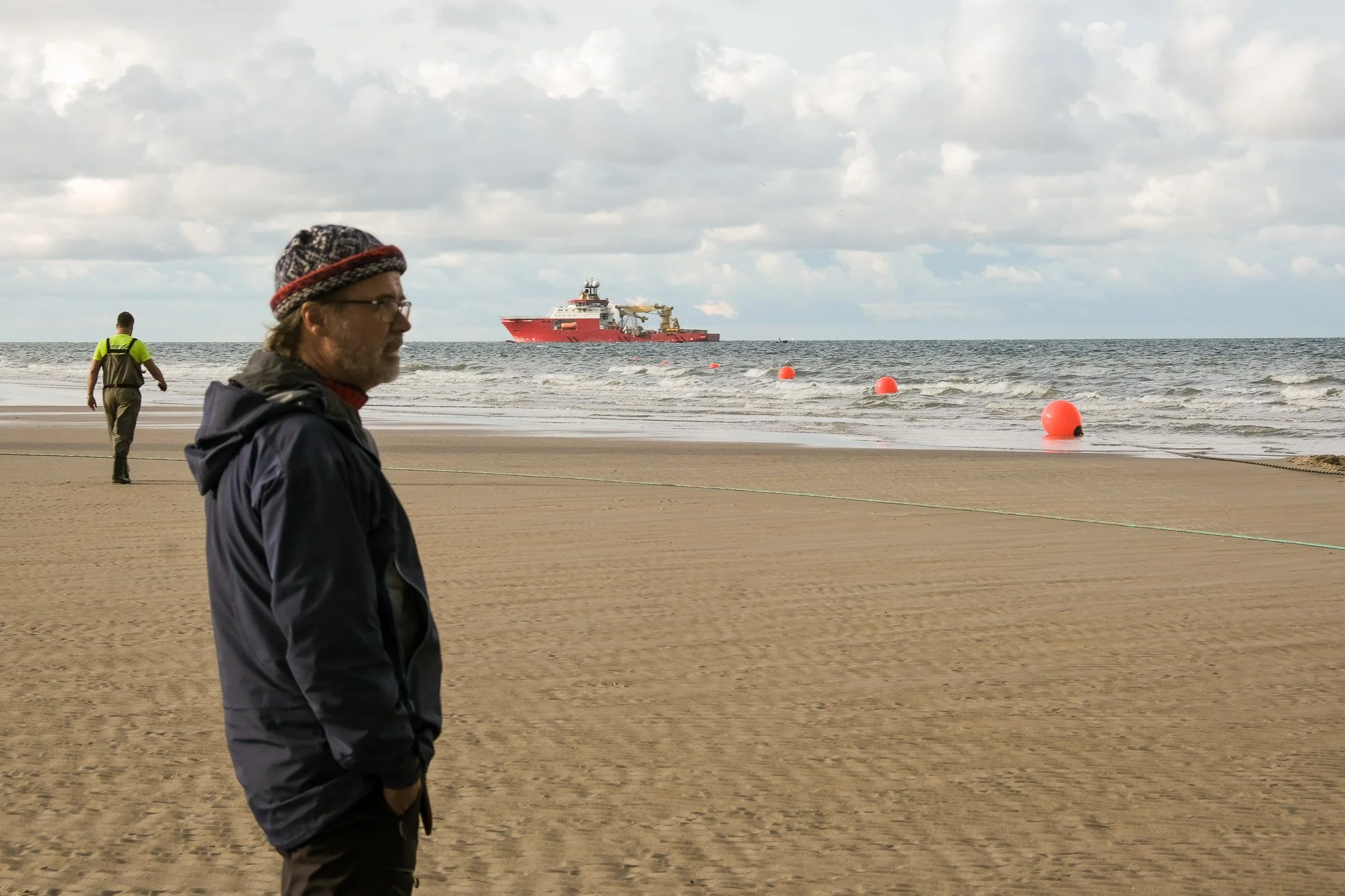
Making ends meet
The subsea fiber optic cable Skagen fiber West went from idea to realisation in four years. 3FM Consult, (now DataEnergy) delivered the turnkey project. Remarkable timing, cost-saving planning combined with applaudable engineering. The team pioneered jet-trenching in subsea cable laying and the terrestrial cable pushed build quality to unprecedented levels.
In 2016, the cheapest renewable energy in the world failed to attract large-scale data centers to Norway due to a lack of connectivity
Skagenfiber AS was founded in 2016. The team had over 20 years of experience building telecom networks, data center constructions, and fiber installations.
They completed the new fiber connection, spanning 145 km of terrestrial and 170 km of submarine fiber optic cable between Oslo, Norway, and Hirtshals, Denmark by November 2020. This project addressed the lack of secure fiber redundancy between continental Europe and thus made Norway an attractive destination for the DC industry.
Because 20% of the world's total electricity consumption may be used by the Internet by 2025, facilitating for data centres where there is renewable power is essential for sustainability. This industry has a perk no other power-consuming industry has, it distributes the product with photons, and it is nearly lossless. That is why the sector should be prioritized for green energy. With the stable operational properties of hydropower, Norway is especially suited for this. Utilizing the electricity close to where it is generated eliminates the significant transition loss in the electric grid. To meet Europe’s future demand for computing, it makes more sense to send photons over nearly lossless fibre cables, rather than electrons over long distances with 20%+ loss of energy.
Rigorous planning for cable economy, working closely with contractors.
One cable stretching more than 170km without a single splice. With elaborate seabed studies, the team managed to route an incredibly accurate plan and find clever new ways of handling the cable. Skagenfiber CTO Rune Skow boards the cable-laying vessel, being hands-on in every decision on the 21-day voyage. The cable was buried 1-2m below sea bottom all the route. As COO Helge Gallefoss took charge of the cable landing, designed and project managed the landing stations.
Building a brilliant team for the project execution
Successfully negotiating large contracts on fair terms and building a team of driven and talented contractors was pivotal to the project and something we take great pride in.
Efficiently preparing for the voyage across Skagerak
The Polar King is refitted for the subsea construction job in Eydehavn, Norway. The custom cable drum is one of many cleverly engineered solutions provided by subsea contractor Cecon, holding the whole 170+ km of Nexans reinforced fibre optic cable. Perfectly calculated, the drum is lifted on board as one single unit, saving days of crewed docking time, which it normally takes to spool a cable of this dimension onboard.
Terrestrial construction begins, with us overseeing every step of the way.
David Gallefoss coordinates planning, documentation, permits, and QC between entities involved in the project.
Contractors Herolf Hansen & Sønn AS and Netel AS embark on the terrestrial cable construction alongside E18, working night shifts to avoid traffic. David joins every night shift to document a total of 500 manholes, mapping the exact position over a 140km stretch and planning where to splice for optimal cable economy with our digital tools.

Built on time and budget. by being hands-on every day, ad-hoc engineering solutions.
Working alongside nature on a big infrastructure project is unpredictable and full of surprises. Decisions have to be made ad-hoc to maintain progress and secure budgets.
The 2020 COVID situation was challenging, travel and deliveries were restricted, but we managed to build on time and budget.
Creative solutions based on great technical skills have to be found and implemented to secure the install and keep control over expenses. A team of approximately 120 persons was involved, and the running cost of the installation ship was approaching 100K EUR per day. Unnecessary delays had to be avoided.